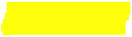
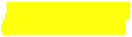
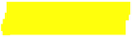
TRATTAMENTI TERMICI
Dopo la lavorazione per asportazione di truciolo i perni subiscono un trattamento termico a seconda delle richieste del cliente si realizzano trattamenti termici di:
cementazione o carbocementazione tempra e rinvenimento per profondità 0,8 mm e HRC 59-62;
La carbocementazione (UNI 5381) o piu comunemente "cementazione" e' attualmente il processo di diffusione maggiormente impiegato a livello industriale. Esso consiste nella carburazione superficiale di particolari in acciaio a basso tenore di carbonio (max. 0.20%) ad una temperatura pari ad Ac3+50°C, comunque generalmente compresa tra 850°C e 950°C.
La carburazione puo' avvenire tramite un mezzo polverulento, pastoso, liquido o gassoso di particolare composizione chimica in grado di garantire un arricchimento superficiale di carbonio che acquisirà poi un'elevata durezza (60-62 HRC) con il successivo trattamento di tempra, conservando al nucleo la resilienza originaria. Il trattamento è pertanto destinato agli organi meccanici che debbono accoppiare alla durezza superficiale e resistenza all'usura, la resistenza a fatica (l'aumento di volume dello strato cementato e temprato legato alla trasformazione martensitica dell'acciaio arricchito di carbonio induce tensioni di compressione dello strato superficiale incrementando notevolmente il limite a fatica).
Dopo il trattamento di cementazione vero e proprio i pezzi devono essere temprati e successivamente rinvenuti, allo scopo di conferire alla superficie le necessarie doti di durezza e resistenza all'usura ed al cuore una soddisfacente tenacità e resistenza a fatica.
I pezzi di lunghezza più elevata devono subire sicuramente una raddrizzatura che renderà più costoso il trattamento.
I particolari che hanno una filettatura da proteggere vengono gestiti internamente e preparati dal nostro magazzino al meglio per subire questo tipo di trattamento.
Procedimenti di cementazione:
1- nel mezzo solido i pezzi vengono posti in cassette metalliche piene di polveri, costituite da carbone di legno con una % del 25% di sostanze acceleranti del processo di cementazione (attivatori) ad una T di 900-950 °C
VANTAGGI: semplice esecuzione e riuscita e modesto costo dell'impianto
SVANTAGGI: elevata durata del processo con formazione di grani grossi, distorsione dei pezzi ed elevata ossidazione superficiale. Scarsa uniformità di spessore dei strati cementati
Tale processo viene eseguito per pezzi singoli o piccolissime serie che non richiedono particolari caratteristiche.
2- nel mezzo liquido si utilizzano bagni di sali fusi. Questo procedimento è praticamente sparito a partire dagli anni '80 per motivi di natura ecologica
3- il mezzo di cementazione che attualmente viene maggiormente sfruttato a livello industriale è quello GASSOSO. Grazie a particolari forni in grado di gestire l'intero processo termochimico, oggi è possibile controllare con estrema precisione tutte le movimentazioni dei particolari all'interno dell'impianto ma soprattutto gestire con assoluta precisione l'atmosfera carburante in camera di trattamento.
VANTAGGI: processo controllabile e veloce. Miglior tipo di cementazione dal punto di vista qualitativo
SVANTAGGI: costo dell'impianto
Dopo la cementazione si deve sempre procedere al trattamento di tempra per ottenere sul bordo cementato la massima durezza possibile e al cuore resistenza e tenacità.
I procedimenti sono:
1- tempra diretta Si tempra il pezzo all'uscita del mezzo cementante e senza un raffreddamento preventivo fino a temperatura ambiente. E' indicato solo per quei pezzi che non sono soggetti ad urti o a sollecitazioni meccaniche importanti in quanto generalmente abbiamo grano ingrossato che provoca fragilità del materiale.
Tale trattamento è il più vantaggioso dal punto di vista economico.
2- tempra unica Si effettua sul pezzo
La tempra unica può avvenire secondo i cicli (1) o (2)
Ciclo (1): riscaldamento di tempra a temperatura superiore ad Ac3 del bordo cementato: si ottiene una grande finezza e tenacità del bordo cementato; tuttavia il cuore, non essendo rigenerato né temprato, presenta resistenza bassa e resilienza incerta perché la struttura non è ben definita. Quindi esiste la possibilità che il pezzo sia fragile.
Ciclo (2): riscaldamento di tempra a temperatura superiore ad Ac3 del cuore: il nucleo, completamente rigenerato e temprato, sviluppa il massimo delle sue proprietà di resistenza e tenacità. Il bordo cementato è invece a grano grosso, perché temprato a temperatura troppo elevata in base al suo contenuto di C.
In pratica, la scelta della temperatura di tempra viene fatta in funzione della zona che si vuole privilegiare e del materiale da trattare.
3- la tempra doppia consiste nella combinazione di due tempre: la prima adatta al nucleo, l'altra adatta alla parte esterna: questo trattamento, in cui si affina il grano sia alla superficie sia al cuore, si presta particolarmente per acciai a grano grosso.
Si nota però che la seconda tempra, effettuata per affinare il grano sulla superficie carburata, distrugge, almeno parzialmente, gli effetti della prima tempra al cuore, provocando un rinvenimento, se non una ricottura del materiale, diminuendo così la resistenza a fatica. Questo trattamento è inoltre il meno vantaggioso dal punto di vista economico.
Dopo tempra, qualunque sia stato il ciclo, è necessario eseguire una distensione a bassa temperatura ( 180 - 200 ° C ) per eliminare le tensioni interne, senza diminuire la durezza del bordo.
Sarà anche necessaria un'operazione di rettifica, per portare il pezzo alle dimensioni e alla rugosità previste in sede di progetto.
Spessore efficace di cementazione
Si definisce spessore efficace la distanza tra la superficie esterna del pezzo cementato e temprato e il punto interno la cui durezza è convenzionalmente HV1/15/550.
Si intende invece per spessore totale la distanza tra la superficie del pezzo e il punto in cui non si rileva più alcuna differenza tra le caratteristiche chimiche e fisiche del cuore e dello strato indurito (lo spessore efficace è circa 2/3 dello spessore totale).
Nitrurazione o carbonitrurazione per prof. 0,2-0,6 mm HRC 58-60.
La nitrurazìone è un trattamento termochimico con azoto, effettuato sui materiali ferrosi in campo ferritico, cioè a temperatura compresa tra 450 e 550 °C per un periodo di tempo che va da qualche ora a parecchie decine di ore, in funzione dello spessore di nitrurazìone che si vuole ottenere.
I processi di diffusione sono tanto più rapidi quanto più elevata è la temperatura perchè è maggiore l'energia degli atomi: operando con temperature relativamente basse (circa 500°C) i tempi del processo saranno più lunghi.
Il mezzo nitrurante può essere un'atmosfera gassosa a base di ammoniaca, un gas a base di azoto allo stato di plasma o anche un bagno di sali fusi a base di cianuri.
Scopo del trattamento è l'indurimento superficiale di un pezzo, per spessori di qualche decimo di millimetro, per migliorare la resistenza all'usura e alla fatica sfruttando il fenomeno d'indurimento per precipitazione, senza alcuna necessità di tempra martensitica.
Gli acciai destinati alla nitrurazione hanno il tenore di C proprio degli acciai da bonifica e contengono alcuni elementi, quali Cr e Al, che hanno il compito di facilitare l'assorbimento e la diffusione dell'azoto. Se questo non avvenisse si formerebbe uno strato molto sottile superficiale e molto duro che non lega col cuore del pezzo. Questa situazione potrebbe essere pericolosa perchè un colpo al pezzo potrebbe togliere questa parte superficiale (sfarinatura).
Inoltre elementi di lega quali Cromo, Vanadio e Titanio formano dei nitruri incrementando enormemente la durezza fino a 1200 HV
La nitrurazìone è generalmente preceduta da un trattamento di bonifica.
Perché la nitrurazìone sia possibile è necessario che:
• il ferro sia allo stato alfa: in caso contrario, l'indurimento sarebbe inferiore; l'azoto ha come effetto quello di abbassare la temperatura di trasformazione da alfa a gamma e con la concentrazione di azoto tipica del processo il Fey è stabile già a 585 °C; è quindi necessario riscaldare a temperature più basse di tale valore;
• l'azoto sia allo stato atomico.
Spessore di nitrurazione
Si definisce spessore di indurimento totale (NtT) la distanza tra la superficie esterna dello strato indurito e il punto in cui non si rileva più alcuna differenza nei valori delle durezze.
Si definisce spessore di indurimento efficace (NtE) la distanza tra la superficie esterna dello strato indurito e il punto in cui la durezza di questo assume il valore convenzionale di 100 HV più del cuore.
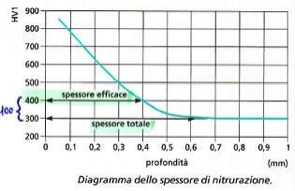
La nitrurazione ha i seguenti vantaggi rispetto alla carbocementazione:
- durezza superficiale più elevata (HV1000-1200 in confronto a circa HV850);
- trattamento finale che non induce ossidazione o deformazione dei pezzi;
- assenza di pericolo di ingrossamento del grano cristallino nel corso del trattamento.
Contemporaneamente, gli svantaggi rispetto alla carbocementazione sono:
- strato indurito più sottile e quindi minori carichi specifici sopportabili;
- ciclo di produzione più lungo e costoso;
- acciai da utilizzare più costosi a causa degli elementi di lega presenti.
Tempra superficiale ad induzione ad alta frequenza per prof. 3-5 mm HRC 55-60.
E' il trattamento che riscalda alla T di austenitizzazione la zona che si desidera indurire facendo subito dopo una tempra martensitica e una distensione.
Tale processo ha lo scopo principale di migliorare la resistenza all'usura e alla fatica e vi si ricorre in particolare nei casi descritti di seguito.
• Necessità tecnologica di indurire solo alcune superfici, come camme, steli di valvole o altro.
• Necessità di contenere le deformazioni: i pezzi di forma complessa sono facilmente soggetti a distorsioni se trattati in maniera convenzionale: con la tempra superficiale possono essere induriti soltanto nelle zone strettamente necessarie, riducendo così il rischio di deformazioni.Si ottiene ponendo il pezzo nel campo elettromagnetico prodotto da una bobina percorsa da corrente alternata.
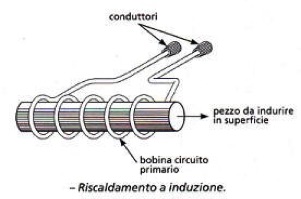
Le correnti indotte dalla bobina tendono a portarsi alla superficie del pezzo e ne provocano il riscaldamento per effetto Joule. L'effetto pellicolare è tanto maggiore quanto più alta è la frequenza della corrente indotta, quindi, regolando opportunamente la frequenza, si può variare lo spessore riscaldato e di conseguenza la profondità di tempra.
Tempra a cuore generalmente effettuata su acciai 42CrMo4 o 100Cr6, HRC 55-62.
Il trattamento termico di tempra degli acciai consiste nel riscaldare l'acciaio al di sopra del punto critico A3, come dimostra il diagramma in acciaio, nel mantenerlo a tale temperatura per un tempo sufficiente ad assicurare la completa trasformazione austenitica in tutte le parti del pezzo e nel raffreddarlo rapidamente in modo che assuma struttura martensitica. Questa è caratterizzata da elevata durezza, ma anche da notevole fragilità: è perciò necessario far seguire al trattamento di tempra un trattamento di rinvenimento, che ne attenui gli effetti. Per la scelta della temperatura di tempra è necessario conoscere con buona approssimazione il punto critico A3, che varia col tenore di carbonio e degli elementi di lega dell'acciaio: la temperatura ottimale si situa a una cinquantina di gradi al di sopra di A3 e non deve salire oltre per evitare l'ingrossamento del grano cristallino, che si traduce in un peggioramento delle caratteristiche del materiale.
Il raffreddamento rapido necessario per la tempra dell'acciaio si ottiene mediante immersione del pezzo in un mezzo di tempra: i mezzi di tempra comunemente usati sono, in ordine di drasticità decrescente, acqua o sue soluzioni saline, olio, sali fusi, aria. La scelta è condizionata dal tenore degli elementi di lega dell'acciaio e dalle dimensioni del pezzo: infatti quanto più elevato è il tenore degli elementi di lega, tanto più spostate verso destra sono le curve di trasformazione dell'austenite e risulta perciò possibile avere trasformazione martensitica anche con velocità di raffreddamento relativamente modesta. Quest'ultima situazione risulta vantaggiosa perchè quanto più rapido è il raffreddamento tanto maggiori risultano le tensioni interne, che rimangono nel pezzo in seguito alla trasformazione austenite martensite, e la possibilità di criccature e rotture. Se l'acciaio contiene notevoli percentuali di elementi di lega può essere temprato per semplice raffreddamento all'aria, e per tale ragione si dice autotemprante. Al contrario acciai non legati e con tenori molto bassi di carbonio (acciai dolci) non possono essere temprati, perchè non è praticamente possibile ottenere raffreddamenti sufficientemente rapidi, essendo le curve di trasformazione molto spostate verso sinistra. Durante il raffreddamento la parte esterna del pezzo, a contatto col mezzo di tempra, si raffredda più rapidamente della parte interna (cuore): pertanto essa inizia la trasformazione austenite martensite prima del cuore e, poichè tale trasformazione avviene con aumento di volume, l'espansione della zona interna è ostacolata dallo strato superficiale già martensitico. Per evitare eccessive tensioni interne, con pericolo di rotture, è stato messo a punto un trattamento che viene denominato tempra differita martensitica.
Nella tempra differita il raffreddamento è effettuato in due tempi immediatamente successivi con due mezzi di diverse tempre: il pezzo viene dapprima immerso in un bagno di sali fusi a temperatura di poco maggiore di quello di inizio della trasformazione e mantenuto a tale temperatura per un tempo sufficiente a realizzare uniformità di temperatura, ma non tale da provocare l'inizio della trasformazione dell'austenite; si procede poi a un raffreddamento fino a temperatura ambiente secondo determinate condizioni, affinchè la formazione della martensite sia pressochè totale.
In taluni casi particolari può essere necessario o preferibile avere, come struttura conseguente al trattamento, anzichè martensite: in tal caso viene effettuato un trattamento denominato tempra bainitica.
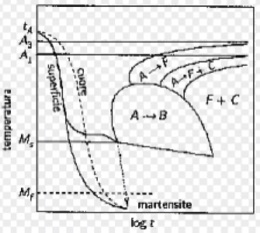
La tempra bainitica può essere eseguita in due modi differenti. Nel primo il pezzo viene riscaldato al di sopra di A3, mantenuto in temperatura per avere la completa trasformazione austenitica, raffreddato velocemente con velocità tale che la traiettoria di raffreddamento attraversi il campo bainitico, così che la struttura finale risulti costituita da martensite e bainite. Nel secondo, dopo la fase di riscaldo e mantenimento, il pezzo viene raffreddato velocemente fino a temperatura maggiore di Ms, mantenuto a tale temperatura fino a che non si abbia la completa trasformazione in bainite, indi raffreddato fino a temperatura ambiente.
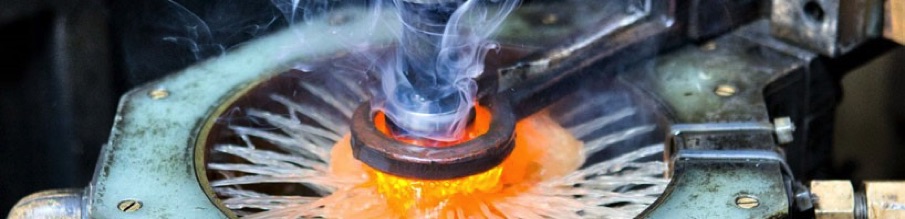